Deep Hardness 1.0
Description:
Deep Hardness 1.0 calculates the micro hardness gradient HV1 necessary to
the contact fatigue resistance, on assuming discontinuities like not metallic inclusions as
nucleation sources for subsurface fatigue cracks, according to the Murakami-Endo theory.
Deep Hardness 1.0 uses the Hertz theory for the calculation of the contact
pressure, then it is valid for cylindrical bodies (absence of convexities)
In case of coupling of materials with different Poisson coefficient, the micro hardness
gradient HV1 in calculated referred to the body with subscript 2.
Conditions:
- The tool does not consider the chemical nature of the inclusion (sulphide or oxide), its degree of adhesion to the metallic matrix and the distribution inside it. The presetted maximum dimension d relative to the bigger inclusion, equal to 50 µm, is considered properly precautionary with respect to the manufacturing methodologies of the modern special structural steels destined to the realization of components subjected to contact fatigue (steels for surface hardening, quench and tempering steels, case hardening steels, nitriding steels with the exception of the RE-SULPHURIZED and ADDED-Pb types. To obtaining a further refining of the calculation it is suggested to follow the DH1 procedure for the determination of d. Only in the case of use of specific steels for bearings it is advised to put d=30 µm avoiding to perform the inquiry defined by the DH1 procedure.
- It is not considered the micro structural variation that is highlighted from the core surface consequent to the specific surface hardness treatment (for example white layers during nitriding, retained austenite during carbonitriding)
- Convexities are not considered
Usefulness:
- Optimization of the surface hardness treatment (costs reductions, reduction of the heat treatment deformations, reduction of stocks from grinding)
- Reduction of the costs derived from prototype and trial
Caution:
- Deep Hardness 1.0 calculates the micro hardness gradient HV1 as a function of the z depth normal to the contact surface. This gradient will give an indication about the surface hardness treatment to choose regarding surface hardness and effective hardening thickness. The micro hardness gradient HV1 vanishes asymptotically, then it is necessary to evaluate what core hardness prescribe as a function of the hardness treatment it will be chosen. For small loads it is possible the tool will return values of hardness simply obtainable with massive treatments, like for example quenching and tempering. The microhardness gradient HV1 always must be interpreted before the prescription of a surface hardness treatment
- For planar cams and bearing races it must be considered, along the whole profile, the heaviest condition in terms of F, D1 and D2
Use:
- Introduce the required parameters in the entry mask
- D1 e D2 : diameters of the osculating circles of the bodies in the contact point respecting the convention of signs of the Hertz theory. For internal surfaces, the diameter is negative.
For the cogwheels these diameters are calculated by the suitable routine putting in the number of frips, the modulus, pressure angle and helix angle of the gear. It is considered the pitch contact point between the frips - F : contact force between the bodies
For the cogwheels the force is calculated introducing the couple that acts on the pinion (wheel 1), besides the dates indispensable to calculate D1 and D2. It is necessary to introduce even the overloading factor (K), used in the measuring of the gear, obtained as a product of the overloading factors relative to each contribution, that is: application load factor (Ka), dynamical factor (Kv), longitudinal distribution of the load factor (Khβ), transversal distribution of the load factor (Khα), according to UNI 8862-1/2:1987 - l : contact width, that is band width of the cam or rolling race. For the cogwheels it is calculated putting in the width b of the gear (it is always intended the overlap width)
- E1 ; E2 ; ν1 ; ν2 : characteristics of the material of the bodies in contact: Young modulus, Poisson coefficients of the bodies 1 e 2
- η : safety factor towards the yielding due to contact fatigue
- μ : friction coefficient between the bodies in contact
- d : maximum dimension of the bigger not metallic inclusion
- D1 e D2 : diameters of the osculating circles of the bodies in the contact point respecting the convention of signs of the Hertz theory. For internal surfaces, the diameter is negative.
- Start the calculation
- Extract the gradient HV1 as a tabulation, define the surface hardness ( HV1 for z=0 ) and the hardness thickness
- Choose the treatment that assure the safety characteristics obtained. The choice is a function of the material, of the geometry and of the dimensions of the component. For the manner of indication in the drawings, please refer to: Drawing Specifications 1.0. In case of difficulty in the choise of the treatment or presence of convexities, please contact info@graniteng.com
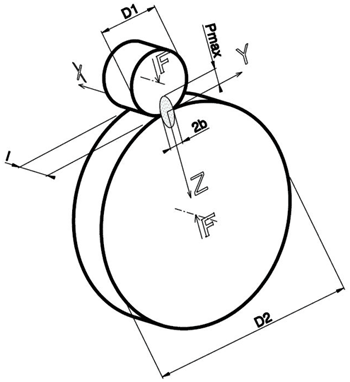
DH1 Procedure
It is necessary to evaluate the micropurity of the steel from which it will be obtained the component subjected to contact fatigue for at least 2 different lots of supplies. The procedure foresees the preparation of n.6 metallographic test samples that they will be observed in optical microscopy without any chemical attack, to mark the maximum dimension d of the bigger not metallic inclusion.- Extract for every product, coming from a single lot of supply, n.3 samples respecting the next indications:
- The testing surface have to be representative of the contact surface of the final component. Then it is necessary to consider the stocks from mechanical manufacturing
- The testing surface have to be parallel the forging, drop forging or rolling direction and belonging to a plane passing for that direction
- The testing surface area cannot be smaller than 100 mm2
- Englobe the n.6 samples now defined (n.3 for each product)
- Pre-rub down and polish utilising methodologies that do not change the shape of the inclusions or undermine them from the metallic matrix (UNI 3137:1965)
- Observe the testing surfaces with a magnification of 100X without metallographic attack, noting for each metallographic test bar the maximum dimension of the bigger inclusion observed
- Introduce in d the value in µm of the maximum dimension of the bigger inclusion observed in the n.6 examined metallographic test samples
In the following it is represented the modality of drawing of samples from a forged rod from which it will be obtained a rolling race for a roller bearing. R-R1 is the stock of manufacturing.
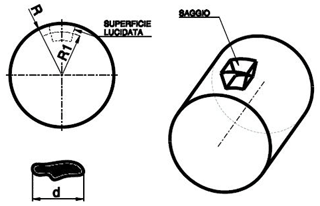
OUTPUT: GEOMETRIC PARAMETERS AND CONTACT FORCE | ||
---|---|---|
D1 [mm] | Osculating circle diameter wheel 1 | 29.93 |
D2 [mm] | Osculating circle diameter wheel 2 | 42.75 |
F [N] | Contact force | 21259 |
l [mm] | Contact width | 36 |